Muovere i primi passi verso una digitalizzazione di successo
Pubblicato il 12 novembre 2024 a Industry 4.0
Perché digitalizzare la produzione?
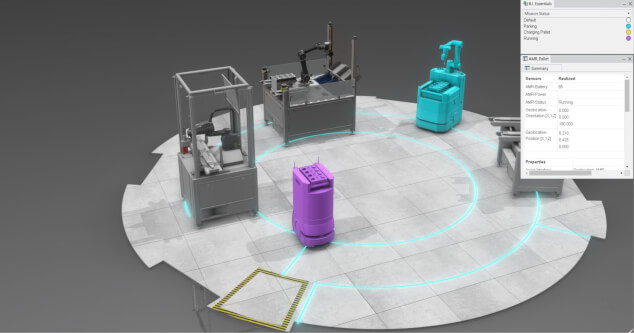
Creando un modello virtuale di una nuova macchina o linea, è possibile contenere i rischi associati ai progetti e ridurre drasticamente il tempo necessario per costruire e testare l'installazione, perché gli errori più costosi vengono commessi nel mondo virtuale anziché in quello reale. Ciò costituisce un vantaggio per qualunque industria manifatturiera, ma risulta particolarmente evidente nel campo dell'automazione, che avverte un'esigenza pressante di accelerare il time-to-market e ridurre al minimo il rischio di errori per i nuovi prodotti.
I vantaggi della digitalizzazione non terminano con la messa in servizio virtuale. Questo è solo l'inizio. Il gemello virtuale rispecchia il sistema fisico in tempo reale e può essere utilizzato per tutta la durata di un sistema o di un prodotto, quindi c'è sempre l'opportunità di verificare, in un ambiente digitale parallelo sicuro, il comportamento di nuovi materiali, nuovi ingredienti o nuovi strumenti.
Inoltre, il monitoraggio continuo della macchina o del processo può essere incanalato per scopi di manutenzione preventiva, monitoraggio delle condizioni, gestione dell'energia e OEE (Global Equipment Effectiveness).
La produzione digitalizzata è anche un prerequisito del lot-size-one, il concetto di essere in grado di produrre qualsiasi prodotto in qualsiasi variante, quantità e sequenza. Questo approccio sta diventando sempre più un elemento di differenziazione nell'industria farmaceutica, dove l'aumento dei farmaci orfani e l'arrivo di una diagnostica all'avanguardia consentono ai pazienti di essere trattati con il farmaco migliore alla dose ottimale per loro.
La digitalizzazione offre un modo per ridurre i rischi, accelerare l'aumento della produzione e creare una flessibilità senza precedenti nei modelli di business.
Come digitalizzare la produzione?
La chiave per realizzare una fabbrica digitale è collegare i due mondi IT e OT. Per anni, questo è stato considerato impossibile data la loro diversità, come se si dovesse cercar di far dialogare marziani e venusiani.
In una fabbrica digitale, tutto, dai sensori al sistema di smistamento, deve far parte di una rete di fabbrica. Ma non è sufficiente che le funzioni siano connesse perché devono anche essere in grado di generare dati e condividerli tra loro. E devono anche sapere come interpretare e processare quei dati. Ad esempio, se al sistema di smistamento viene comunicato che non è disponibile una plastica e che verrà fornito un materiale sostitutivo con specifiche tecniche leggermente diverse, la funzione di smistamento deve comunicarlo alla linea in modo che le impostazioni della macchina possano essere regolate di conseguenza. I sistemi fisici informatici sono gli elementi costitutivi di queste reti, garantendo il collegamento tra i vari componenti.
L'autoapprendimento e i sistemi adattivi sono un altro pilastro del successo della digitalizzazione. Vengono infatti applicati degli algoritmi di apprendimento automatico per elaborare grandi volumi di dati relativi a prodotti, linee e macchine. Ciò consente ai produttori di ottimizzare gli aspetti del processo di produzione che richiedono molto tempo, tra cui il controllo della qualità, la manutenzione delle apparecchiature e la progettazione dei prodotti.
L'altro fattore critico di successo è far cooperare umani e macchine, lavorando in armonia. Sfruttando l'intelligenza artificiale e la robotica, i produttori possono trarre vantaggio dalle interazioni tra esseri umani e macchine, portando la produzione a un nuovo paradigma di flessibilità e personalizzazione.
Tutto questo dipende fortemente da collaborazioni intense e a lungo termine. Di fatto, l'unico modo per l'industria manifatturiera di sfruttare il potenziale della digitalizzazione è che esperti di diverse specializzazioni lavorino insieme. Ciò può comportare la creazione di partnership con clienti, fornitori, provider di servizi, aziende di altri settori, istituti accademici, startup e persino concorrenti. Questi tipi di collaborazione si traducono in ecosistemi aziendali complessi e sinergie in grado di generare soluzioni rivoluzionarie.
Si tratta di un approccio che richiede apertura. La maggior parte dei costruttori di macchine si rifiuta di rivelare la funzionalità interna delle loro macchine perché temono di svelare il segreto di ciò che le rende uniche sul mercato. Ma l'unico modo per unire i due mondi di OT e IT è creare ecosistemi che operino sulla fiducia reciproca.
Il partner di OMRON nella progettazione della produzione digitale è Dassault Systems. Quando le capacità di entrambe le aziende si sovrappongono al modello funzionale ISA-95, spesso chiamato framework per la progettazione della fabbrica digitale, si crea una soluzione ideale, ovvero un modello ISA completo pieno di competenze combinate.
La digitalizzazione ha un ruolo indiscutibile nel garantire flessibilità e personalizzazione sempre maggiori, cicli di innovazione più brevi e una produzione più sostenibile in una vasta gamma di settori manifatturieri. In un futuro non tanto lontano, ci aspettiamo di vedere che tutto, dai veicoli elettrici e gli antibiotici, fino ai cioccolatini e ai rossetti, sia prodotto nelle fabbriche digitali.
Contattaci per ulteriori informazioni